The SpinTron – The Racer’s Edge in Valve Train Development
SpinTron Roller Tappets, Rockers and Friction Testing
From our friends at Goodink and Jesel, here’s your chance for an inside look into the highest performance race engine component development and the special equipment needed to break records at Bonneville or in the NHRA. In this case, it’s a dyno, it’s got a laser… it’s SpinTron! – pikesan

The SpinTron roller tappets and rocker arms tester
Story by: Ray T. Bohacz
Jesel, one of the best competition valve train specialists to emerge in the past thirty years, owes much of its supremacy to extensive developing and testing of its competition parts. The test machine is a SpinTron. The parts being tested are principally roller tappets and rocker arms.
“Ten or twelve years ago when I first pressed the SpinTron into action,” says Danny Jesel, “my immediate response was one of shock—the racket it generated was incredible! I just wasn’t expecting the opening and closing of two valves to be so loud, and initially I thought something was broken.”
Once Danny Jesel became accustomed to the commotion, his next challenge was grappling with the phenomenon known as “lofting”. Lofting occurs when engine speeds increase, usually above 4,000rpm, causing the tappet and valve train components to lose contact with the camshaft each revolution. As a result the valves remain open much longer than camshaft designers had intended.Some race engine developers call it “controlled valve float.” “I was intrigued,” admitted Danny, “as I observed the valve gear components soaring over the nose of the camshaft by a distance greater than 0.100in above the lobe. It fascinated me, and I initially thought this thing called lofting will create havoc in the shortest period of time. But it didn’t. As I watched the SpinTron tracing the valve events, it became intriguingly predictable. I began to think of it as a ball connected to a bat by an elastic cord, and if you smack the ball with the same force each time, its travel through space will repeat.”
Although Jesel, a manufacturer, acquired their SpinTrons to test the durability of their valve train parts, most of these remarkable test machines are in the hands of the country’s leading engine builders. To stay ahead of their rivals, engine builders and professional race teams use them to gain vital data. Whether they are gathering information on valve train performance or calculating frictional losses within the engine, transmission, or final drive, they are aware that knowledge is power, and having access to SpinTron data is a good first step. “How else can you explore beyond normal mechanical limits of race engine development without provoking a trail of devastation,” says SpinTron creator Bob Fox. Cause and Effect: The Study of Valve Response to Cam Lobe MotionAdvanced engine development, either for the race track or at the OE level, depends on the ability to test and simulate real-world conditions while in the laboratory. Only in a controlled and repeatable environment can accurate data be gleaned. Certain areas however, such as the study of the valve train while it operates at high engine speeds, have denied close examination until fairly recently. The SpinTron by Trend Performance changed all of that—the behavior of every component responsible for valve actuation (either OHV or OHC) can now be examined, imaged, and graphed in real time for analysis. The SpinTron was born of necessity by Trend Performance’s owner and founder Bob Fox. Wanting the ultimate push rod for racing applications, there seemed no way to improve its design other than hit-and-miss dyno testing. And when pushrod failure did occur, the reason was often unknown. For valve train technology to move forward, Fox recognized that a means to study the valve’s response to the profile of the camshaft was necessary. The SpinTron quickly revealed what was believed to be happening in the valve train was not the case. The proverbial book on valve train dynamics needed to be completely rewritten, and the SpinTron would be the author. Armed with a cost-effective device that obtains accurate valve train analysis, racing teams and engine builders along with original equipment manufacturers began to embrace the SpinTron. There was a collective response within the industry, particularly within Nascar circles, for the virtues of this test fixture. But despite the progress it pioneered in the past fifteen years, many engine builders are still unfamiliar with its workings and benefits—benefits available to engine development programs at any level. For this reason Engine Builder magazine prepared this primer establishing the basic function, design, and operation of the SpinTron. The SpinTron ComponentsAt first glance the SpinTron resembles an engine dyno. There is, however, one huge difference—where the water brake would reside there is a large electric motor concealed in the apparatus’s sheet metal housing. Instead of the engine working against a brake, the electric motor spins the crankshaft which in turn runs the engine without fuel, ignition, or combustion. The data acquired during the test procedures is processed and stored in the SpinTron’s computer. When the test engine is mounted on the Spintron it is fitted with a mandrel (dummy crankshaft) and a lubrication system. The lubricating system can be either of SpinTron origin or alternately of a conventional dry-sump arrangement, as depicted in this story. There are two principal versions of the SpinTron: a gear-reduction model and a direct-drive model. The gear-reduction model, which is the most prevalent, is used principally for valve train testing and is offered with one of four electric motors: 25, 50, 75, or 100 horsepower. On the other hand the direct-drive model is equipped with a 150-, 200-, or 250-horsepower motor. It is used for spinning the entire engine, including pistons, and its principal function is to determine frictional loses. With an optional torque arm attachment this more powerful machine has the capacity to measure torsional deficiencies of internal components. The gear-reduction machine operates up to 11,000 rpm whereas the direct-drive model, which uses liquid-cooled electric motors, operates up to 12,000 rpm. Regardless of the model of SpinTron, valve train analysis can be performed as a function of a Laser Valve Tracking System (LVTS) or, alternatively, through a very high-speed camera that captures up to 4,000 frames per second. The LVTS provides measurable data, for example, data displayed on a graph showing the magnitude and duration of valve openings referenced to the crankshaft position. The high-speed camera allows valve events to be viewed but not measured. In addition there is an optional high-speed data acquisition system boasting 16 differential 16-bit analog inputs, 250 KHz acquisition rate, 2 pulsed inputs of up to 5 MHz and 2 encoder inputs. The 16-bit analog input option relates to the number of sensor signals the machine’s high-speed data acquisition system can receive. For example, you might wish to monitor a load gauge under a valve spring or, perhaps, observe the differential signal of an oil temperature sensor. This high-speed optional acquisition system converts the differential signal to an intelligible gauge reading. The term 250 KHz reveals how fast the Spintron receives and stores its information. The encoder is used to identify the position of the crankshaft, and the two pulsed inputs permit the use of two encoders which, for example, could be used to determine torsional deficiencies in a part. Other functions such as a 16-digital I/O (input/output) signal, a termination board and oscilloscope can be added. The oscilloscope allows valve motion to be observed in real time. Additional sensors to measure flow, pressure, vacuum, temperature, and knock can also be integrated into the SpinTron. Accordingly, any or all of this data can be acquired during testing and, importantly, recorded on a report. A work station console is offered as an option or the operator can choose to run the SpinTron though a laptop or PC with the dedicated software. For endurance testing, other custom accessories can be ordered for your engine program. Laser Valve Tracking TestingThe most common use of the SpinTron is testing with the LVTS. To perform this task a window is cut into the engine block and the laser head is inserted in the cylinder bore facing upward at the head of the valve. The results of the valve’s behavior will then be displayed on a graph referenced to the crankshaft position. The common custom for using the LVTS is to first create a baseline of the valve’s action at a low rpm, when the valve’s opening and closing events will repeat precisely the profile of the cam lobe. Baselines are typically established at 2,000 to 3,000 rpm. Then, through the control software, engine speeds are increased in increments of your choosing. The SpinTron will record each new valve trace over the baseline trace. This practice, known as step-testing, performs complete valve train analysis, providing the ideal conditions to compare valve train stability at different engine speeds. It detects events such as valve bounce; lofting (that is, when components of the valve train lose contact with each other due to inertia); harmful spring harmonics; and pushrod deflection. It also identifies weaknesses, design flaws, and misbehavior that will not only cost horsepower but reliability as well. Another important area of research is endurance-testing or cycle-testing where every gear change and every rpm over the duration of a race or over thousands of road miles can be simulated. In common with step-testing, the SpinTron can record and graph data from a variety of sensors at different engine speeds. This provides an excellent opportunity to test a host of components like a fuel pump or an oil pump, as it will record vacuum or flow or pressure during each segment of a lap. Running comparison tests is also effective, particularly comparing different valve springs. Through advanced software, dedicated race track simulation can be created without the risk of engine wear or failure and without any fuel or vehicle required. None of these components are needed to perform SpinTron testing. Seeing is BelievingTo gain practical exposure to the SpinTron, Engine Builder magazine traveled to Lakewood, New Jersey, and visited the facility of Jesel Valve Train. There we met Walter Donovan, a humble man with exemplary credentials, who provided us with a demonstration of the SpinTron. Walter is an accomplished engineer, a metallurgist and scientist, and one of the individuals responsible for Jesel’s leadership in valve actuation and dynamics. Jesel employs two gear-drive Spintrons, each located in a dedicated cell. Both machines are constantly in use for R&D testing. It is admittedly the one tool that has allowed Jesel to revolutionize the valve train of the pushrod competition engine. When queried about the SpinTron Walter Donovan was quick to state, “Without such a tool the speed of our development programs would have been hampered and our knowledge, particularly of modern valve spring development, would have been severely impeded.” He further stated, “Cylinder head development is a moving target, and to get the most from any improvements in volumetric efficiency, the valve train needs to work properly, and at higher engine speeds. During our early days of testing at Jesel, we were shocked by the dramatic effects of minute changes to the cam or rocker profiles and the impact they had on the valve action and, as a result, on horsepower and rpm capabilities.” After a morning of working with the SpinTron, it is the author’s opinion that a valve train not developed using this equipment is leaving potential gains on the table, and if it works, it is only by chance and not by sound engineering. As race and OE engines continually push the technological envelope for different goals, practical valve train analysis becomes essential in that process. Is the SpinTron for everyone? No. It is only for those that want their engine program to be the best. The others must try to follow.
|
![]() Race engine builders make use of test machines at SpinTron’s Michigan facility. The engine on the SpinTron uses a mandrel instead of its original crankshaft and valve train tests are usually conducted on one cylinder. ![]() The normal lubrication system supplied with the SpinTron comprises: dry-sump oil reservoir, remote oil filter, and oil hoses. An oil pump is also included but not the oil pan. To maintain engine block rigidity, Spintron recommends no more than one cylinder opening per side, in contrast to the engine displayed. ![]() Jesel uses this particular Spintron at their New Jersey factory for valve train study only—chiefly rocker and tappet analysis. For this function they install one cylinder head only. The lifter valley and the left bank of the engine block are sealed so that lubricating oil can be retained. ![]() This particular Jesel test requires just one rocker arm and attendant valve train, operating on a single cylinder. Note the blue hose provides cooling oil to the valve spring. The other fittings function as oil drains. ![]() The laser position sensor, part of the Laser Valve Tracking System (LVTS), provides measurable data to the SpinTron’s computer, which is displayed on a graph showing the magnitude and duration of valve openings referenced to the crankshaft position. ![]() Mounted on a tripod to keep it secure and vibration-free during testing, the laser position sensor is placed in a cylinder through an opening in the side of the engine block. Its red laser dot is aimed at a valve head. ![]() This control box powers the Laser Valve Tracking System. The meter on the left displays the intensity of the laser’s signal; the meter on the right displays the laser’s position; and the meter in the center displays the temperature of the laser position sensor. ![]() The SpinTron’s computer screen displays two valve traces (red and blue) and an inset containing valuable data. The data inset explains the baseline, which is displayed as a blue line and indicates valve movement at 5,451 rpm. The red line represents the data line and indicates valve movement at 9,900 rpm. The baseline height is stated as 1.064in; the data height as 1.109in; and finally a delta reading is given as 0.045in. This simply means that at 9,900 rpm, valve lift is 0.045in greater than at 5,451 rpm. Therefore the valve is lofting by forty-five thousandths of an inch at 9,900 rpm. ![]() The apparatus on top of the SpinTron’s console (under the gentleman’s right hand) is an optional oscilloscope. Although the oscilloscope does not portray a baseline valve trace, it does verify the accuracy of the information transmitted to the computer via the LVTS. ![]() Although the SpinTron is controlled from the console, manual controls are also provided on the side of the unit for engine set up. Positioned at the upper left is a jog button, which allows the SpinTron to be jogged when adjusting valve clearances for example. The indicator light on the upper right glows when the power is switched on. The stop button is positioned on the lower left and a manual oil pump, which is controlled by three settings (off, on, or auto), is located on the lower right. ![]() Ilmor, the distinguished engine developer for racing cars and boats, test their latest Indy marine outdrive. This new outdrive and accompanying transmission were both developed using the Spintron. “We use our Spintron to validate all our new or improved parts including valve springs, each of which is subjected to a 100-hour test before use.” Ian Hawkins, Ilmor Marine. ![]() For a Pro Stock race engine, the Spintron is supplied with a 100 horsepower electric motor. For a less powerful V-8, a 50 horsepower unit is usually sufficient. For a twin cylinder motor cycle, like this remarkable S&S engine, a 25-horsepower unit would be recommended.
|
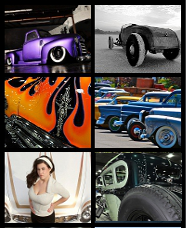